
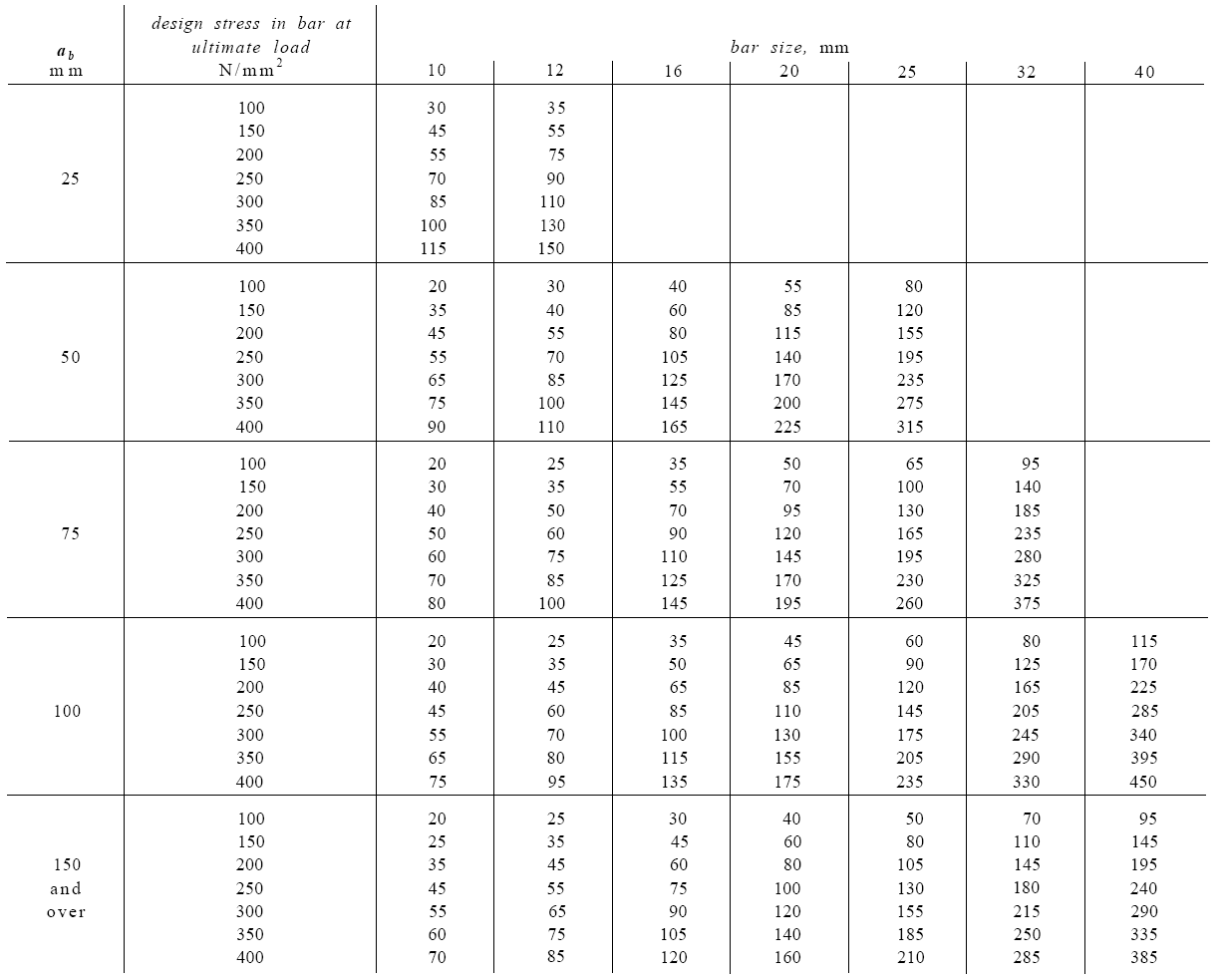
thick, grade 350 and 400 may have a minimum bend radius of 2.5 times the material thickness when transverse bending, while longitudinal bending may require a minimum bend radius that’s 3.75 times the material thickness (see Figure 1).Īlso note that all these are just examples actual minimum radius values vary by grade. The minimum inside bend radius is even larger when bending with the grain.

It’s true that the harder and thicker the plate is, the greater the minimum bend radius. radius is the minimum producible inside radius for this material and not the recommended inside radius that you see on the bend allowance chart. However, I believe you misinterpreted the meaning and how it relates to your bend allowance chart. Minimum Bend Radius vs Recommended Bend RadiusĪ:You have the formula correct at 0.375 in. Is the 20 percent number correct, or did I apply the equation incorrectly? die width.I know you mentioned that the calculation you gave is a rough guide, but the discrepancy between the formula and the brake manufacturer’s bend allowance chart seems significant it’s off by a factor of 2. For 0.5-in.-thick plate, it shows an inside bend radius of either 0.781 in. However, a bend allowance chart I have from our press brake manufacturer gives different information. Then I’d multiply this answer by the material thickness: 0.75 × 0.5 = 0.375 in. Is this the property to which you refer? Using the median of 20 percent and material thickness of 0.5 in., would this equate to × 0.5 = 0.75. So in this case, the minimum inside bend radius is 2 times the material thickness.” If I am looking at properties for A36 steel, I see elongation properties between 18 and 21 percent. If the material is 0.5 inch thick: 4 × 0.5 = 2. Now, multiply that answer by the plate thickness. Next, subtract 1 from that answer: 5 – 1 = 4. To state your example, “If the steel has a tensile reduction value of 10 percent, divide 50 by that value: 50/10 = 5. You described a rough rule to find a steel’s minimum bend radius: Divide 50 by the material’s reduction percentage, as specified by the material supplier, subtract by 1, and then multiply by the plate thickness. Q: In a previous Bending Basics article, you mention a “material’s tensile reduction percentage” used for calculating the minimum inside bend radius of various metals. Grain, increases the required minimum inside radius of Longitudinal bending, or bending with the material
